Our Mission
At Mark 7 Reloading®, innovation drives everything we do. We're redefining the reloading experience everyday with machines we build, all with unmatched speed, precision, and ease of use. Whether you're looking for manual, progressive presses or trying to get into full automation, our products are engineered to work together, providing the ultimate solution for high-volume reloaders.
Proudly designed and manufactured in the USA, nearly every Mark 7 product is a testament to our commitment to quality and innovation. Our team is full of shooters who use these machines themselves, and whom are all passionate about engineering the world’s best reloading equipment, constantly evolving and improving to ensure we're always at the forefront of the industry.
Continued Innovation
Since introducing the original Mark 7® in 2015, we’ve been on a journey of continuous innovation. That same year, we launched the Revolution — the first fully automated reloading press designed specifically for individual users, not just large reloading operations. We followed up with the Evolution, which combined the Revolution's automation with manual operation, giving users more flexibility and control.
In 2020, we introduced the APEX 10, a groundbreaking progressive reloading press that sets new standards in automation and performance. Designed to deliver advanced features at a more accessible price point, the APEX 10 offers exceptional value without compromising on quality. Its robust build quality, combined with the availability of replacement parts, ensures long-term reliability. Many APEX 10 units have successfully processed tens of thousands of rounds, maintaining optimal reloading efficiency throughout, making it a trusted choice for reloaders who demand both performance and durability.
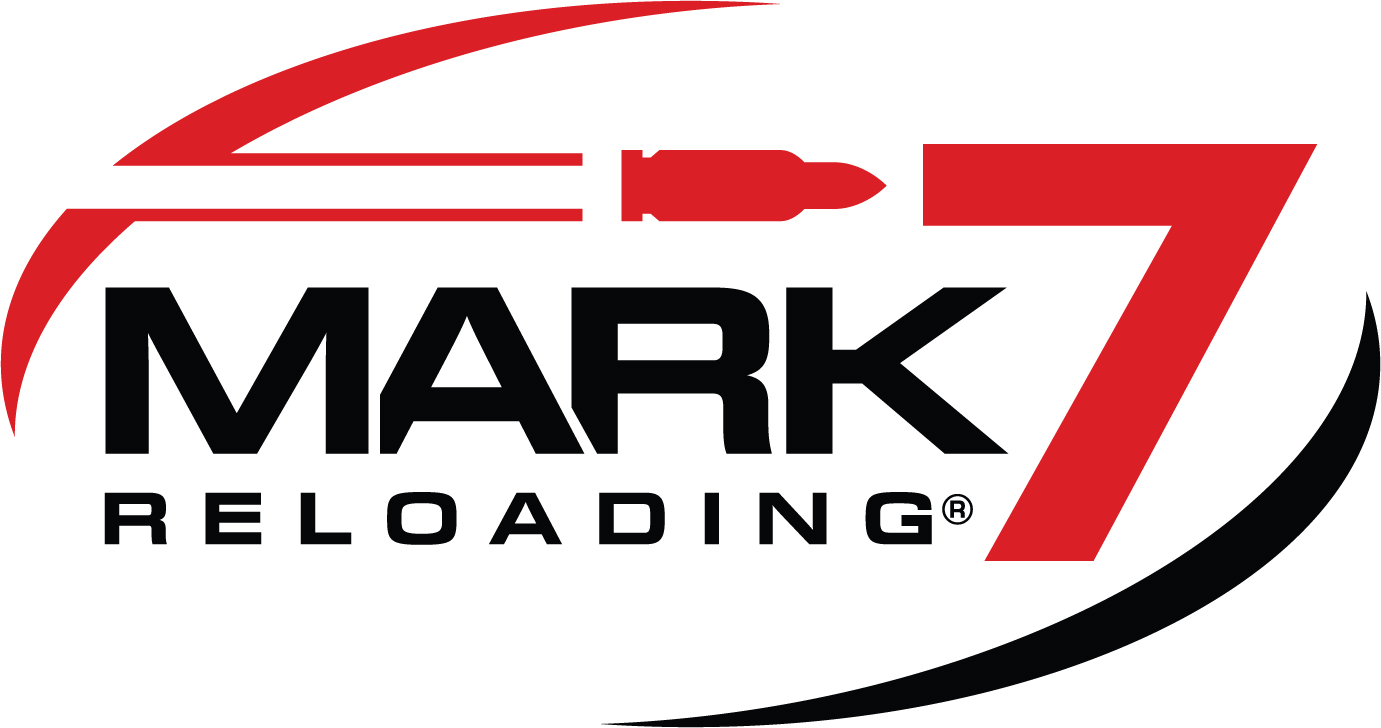
Meet the Team
Tom Carlson
Tom Carlson provides a wealth of hands-on experience and technical expertise at Mark 7 Reloading. As a longtime tactical shooter and NRA Instructor, Tom’s journey into competitive shooting began in the late 2000s, and he quickly developed a deep appreciation for the precision and performance required in the sport. Since discovering USPSA in 2012, he's remained committed to pushing the limits of power, speed, and accuracy—insights he now applies daily in working with customers to find the ideal reloading setup to suit their experience and needs. With in-depth knowledge of every press in the Mark 7 lineup, Tom provides top-tier support to reloaders of all levels, ensuring they have the tools and understanding needed to achieve peak performance.
Conor Craig
Conor Craig brings a lifelong connection to the shooting sports and a hands-on understanding of reloading to the Mark 7 Reloading team. Growing up around USPSA, with both his father and uncle involved in the sport since the early ’90s, Conor developed a deep appreciation for competition early on. After moving to Florida, he began competing himself in 2021 and quickly became immersed in the sport. As an active shooter and dedicated user of the Mark 7 Revolution, Conor leverages his firsthand experience to help others get the most out of their reloading systems. His knowledge of ammunition customization and press performance makes him a valuable resource for both new and experienced reloaders looking to achieve precision and consistency with every round.
John Vlieger
John Vlieger combines extensive competitive shooting experience with hands-on technical knowledge to support Mark 7 Reloading customers in getting the most out of their systems. With over a decade in the sport and more than 150 major matches under his belt, John understands what serious shooters need—because he’s one of them. His background as a U.S. Army veteran and high-level competitor gives him a unique ability to provide practical, on-the-ground assistance for press setup, optimization, and troubleshooting. Whether he’s helping a new user dial in their first automated press or sharing insights through social media, John is a trusted resource and passionate advocate for the reloading community.
Jason Olson
Lorem ipsum dolor sit amet, consectetur adipiscing elit. Ut elit tellus, luctus nec ullamcorper mattis, pulvinar dapibus leo. Lorem ipsum dolor sit amet, consectetur adipiscing elit. Ut elit tellus, luctus nec ullamcorper mattis, pulvinar dapibus leo. Lorem ipsum dolor sit amet, consectetur adipiscing elit. Ut elit tellus, luctus nec ullamcorper mattis, pulvinar dapibus leo.
Lorem ipsum dolor sit amet, consectetur adipiscing elit. Ut elit tellus, luctus nec ullamcorper mattis, pulvinar dapibus leo. Lorem ipsum dolor sit amet, consectetur adipiscing elit.
Autodrives compatible with
Mark 7 and Dillon Presses
How Does an Apex 10 w/Autodrive Stack Up to the Competition?
Apex 10
w/Autodrive
Dillon RL 1000
w/DA 3000
Features
Mark 7 Apex 10 with Autodrive
Dillon RL 1000 with DA3000
Install Time
(Approximation)
30 Minutes,
No need to disassemble press
“A Few Hours” (info from Dillon’s website)
Press must be completely disassembled
Install Time
(Approximation)
Apex 10 w/Autodrive:
30 Minutes,
No need to disassemble press
Dillon RL 1000 w/DA 3000:
"A Few Hours" (info from Dillon's website)
Press must be completely disassembled
Retail Price*
(for Automation)
$2,399,
Sold Worldwide
$1,999,
Sold only in the U.S.
Retail Price
(For Automation)
Apex 10 w/Autodrive:
$2,399, Sold Worldwide
Dillon RL 1000 w/DA 3000:
$1,999, Sold only in the U.S.
Max
Speed
3,500
Rounds per Hour
2,000
Rounds per Hour
Max Speed
Apex 10 w/Autodrive:
3,500 Rounds per Hour
Dillon RL 1000 w/DA 3000:
2,000 Rounds Per Hour
User
Interface
10" Touch Screen Tablet
Dot Matrix Display
User Interface
Apex 10 w/Autodrive:
10" Touch Screen Tablet
Dillon RL 1000 w/DA 3000:
Dot Matrix Display
On the
Fly Adjustments
Overall Speed
Sensors On/Off
Top/Bottom Dwell
Index Speed
Bottom Slowdown
Up/Down Speed via
Forward Facing Knobs
On the Fly
Adjustments
Apex 10 w/Autodrive:
Overall Speed
Sensors On/Off
Top/Bottom Dwell
Index Speed
Bottom Slowdown
Dillon RL 1000 w/DA 3000:
Up/Down via
Forward Facing Knobs
Available
Sensors
DecapSense
SwageSense
Primer Orientation Sensor
Digital Powder Check
BulletSense
Low Powder Sensor
Low Primer Sensor
Does not detect issues during loading,
only availability of components.
Available Sensors
Apex 10 w/Autodrive:
DecapSense
SwageSense
Primer Orientation Sensor
Digital Powder Check
BulletSense
Dillon RL 1000 w/DA 3000:
Low Powder Sensor
Low Primer Sensor
Does not detect issues during loading,
only availability of components.
Clutch
Digital Clutch, User Adjustable
from 0-20 with TorqueSense.
Instant Torque Feedback
Non-adjustable
Overload Protection
Clutch
Apex 10 w/Autodrive:
Digital Clutch, User Adjustable
from 0-20 with TorqueSense.
Instant Torque Feedback
Dillon RL 1000 w/DA 3000:
Non-adjustable Overload Protection
Homing
Function
One button homing,
encoder allows for machine jogging at any time.
Manual home with included wrench.
Anytime machine is stopped,
unit must be manually re-homed prior to restart.
Homing Function
Apex 10 w/Autodrive:
One button homing, encoder allows for machine jogging at any time.
Dillon RL 1000 w/DA 3000:
Manual home with included wrench. Anytime machine is stopped, unit must be manually re-homed prior to restart.
*Retail prices reflect automation only, not including the presses or other accessories, as of November 2024. Pricing is subject to change.
10-Station CNC Toolhead
Allows Unique Reloading Setups
What are the Benefits of 10 Station's?
A common question we receive at Mark 7 Reloading is, "Why do our presses feature 10 stations?" While this may seem straightforward to seasoned reloaders familiar with 7-station presses, it’s not immediately clear to those newer to reloading or progressive systems. The key advantage of a 10-Station toolhead lies in its ability to separate specific die operations, allowing each station to perform a dedicated function for enhanced precision and efficiency. Below are some of the key benefits:
- Separation of Sizing and Decapping
By using a universal decapping die, the decapping pin can be removed from the sizing die and installed over the priming station. This setup not only allows the sizing die to have its own dedicated station, but also enhances the centering and hold-down of the case, leading to more consistent priming. - Separation of Flaring and Powder Drop
Separating these two functions improves both the quality and control of the case mouth flare. This configuration also ensures that the powder measure is solely responsible for dropping powder. Systems that combine flaring and powder dropping can cause brass to stick to the flare plug, which can dislodge when the toolhead lifts, potentially disrupting the powder measure and leading to inconsistent charges. Our powder measures are specifically designed to drop powder, and attempting to use them for flaring can damage the mechanism. - Dedicated Bullet Feeder, Powder Check, Seating, and Crimping Stations
With fewer stations, you may be forced to combine some of these critical functions, which compromises both time efficiency and the overall quality of the reloaded rounds. By dedicating a station to each of these functions, our system saves you valuable time and ensures greater precision, allowing for more effective and consistent reloading without the need to frequently switch dies. - Station Separation Produces Superior Results
Combining critical operations like some other die makers, such as seating and crimping, can result in subpar outcomes, such as bullet jacket damage, which affects both accuracy and consistency. Separating these functions maximizes the potential of each round, ensuring higher-quality ammunition. - Freedom of Customization
Although the 10-Station toolhead offers ample space for advanced setups, you don’t have to use all 10 stations if your current needs don’t require it. For example, if you’re primarily reloading basic pistol ammunition, you can use the 10-Station toolhead as you would any other. The additional stations, however, provide future-proof flexibility, allowing you to expand your reloading setup as your needs grow.
These are just a few of the many reasons why a 10-Station toolhead offers significant advantages for serious reloaders. If you're unsure where to begin, explore our recommended setups below. By clicking on the image of the toolhead or selecting the "Setup" button, you can take a closer look at each individual station and see how the system is designed to optimize your reloading process.
10 Station Toolhead Setup -
Full Loading
This is how you’d set up your tool head when fully loading ammunition.
Overview
10 Station Toolhead Setup -
Loading Primed Brass
This is how you’d set up your tool head on an Apex 10 if you're loading pre-primed brass.
Overview
10 Station Toolhead Setup -
Processing Pistol Brass
This is how you’d set up your tool head on an Apex 10 if you wanted to process pistol brass.
Overview
Station 6: Empty
Station 7: Empty
Station 8: Empty
Station 9: Empty
Station 10: Empty
Station 1: Case Feed
Station 2: Universal Decap Die
Station 3: Universal Hold Down Die
Station 4: Size Die
Station 5: Empty
Station 6: Empty
Station 7: Empty
Station 8: Empty
Station 9: Empty
Station 10: Empty
10 Station Offset Toolhead Setup -
Proccessing & Trimming Rifle Brass
This is how you’d set up your tool head on an Apex 10 if you wanted to process and/or trim rifle brass.
Overview
Station 6: Partial Trimming
Station 7: Empty
Station 8: Empty
Station 9: Trimming
Station 10: Empty
Station 1: Case Feed
Station 2: Universal Decap Die
Station 3: Universal Hold Down Die
Station 4: Size Die
Station 5: Empty
Station 6: Partial Trimming
Station 7: Empty
Station 8: Empty
Station 9: Trimming
Station 10: Empty
Easy Caliber Conversion for
Multitude of Rifle & Pistol Calibers
What's Involved in a Caliber Conversion?
Mark 7 Reloading presses are engineered for relatively easy caliber changes, simplifying the conversion process for users. When switching calibers, it’s important to consider all key components of the press, including the Bullet Feeder, Case Feeder, Powder Measure, Priming System, and various press parts such as the shell plate, case feed ram, and case feed adapter. Depending on your starting and target calibers, some of these parts may remain unchanged. To assist with this process, we’ve provided detailed resources below, outlining exactly which components are needed for each caliber conversion.
Converting Your Case Feeder
Your Mark 7 11” High Speed Case Feeder comes with both large and small Output Springs, and large and small Case Drop Tubes, so the only piece that may need to change is the Case Feed Plate. The plates are available in Small Pistol, Large Pistol, Small Rifle and Large Rifle.
Converting your Bullet Feeder
Converting Priming
Your Mark 7 Apex 10 Manual Priming system comes with either a large OR small priming tube depending on your caliber. If you want to load a different caliber, you'll need to purchase the corresponding Primer Conversion Kit and switch over to that type of tube.
Converting your Press
Depending on calibers, you may need a new Shellplate, Case Feed Ram and Case Feed Adapter. However, some calibers use the same parts. For example, while 9mm and 38 Super Comp require different shell plates, you'll be able to use the same Case Feed Ram and Adapter for both calibers.
Converting Your Case Feeder
Your Mark 7 11” High Speed Case Feeder comes with both large and small Output Springs, and large and small Case Drop Tubes, so the only piece that may need to change is the Case Feed Plate. The plates are available in Small Pistol, Large Pistol, Small Rifle and Large Rifle.
Converting Priming
Your Mark 7 Apex 10 Manual Priming system comes with either a large OR small priming tube depending on your caliber. If you want to load a different caliber, you'll need to purchase the corresponding Primer Conversion Kit and switch over to that type of tube.
Converting Your Bullet Feeder
Converting your Press
Depending on calibers, you may need a new Shellplate, Case Feed Ram and Case Feed Adapter. However, some calibers use the same parts. For example, while 9mm and 38 Super Comp require different shell plates, you'll be able to use the same Case Feed Ram and Adapter for both calibers.
Wide Array of Automated Sensor's
How Can Mark 7 Sensor's Enhance Your Reloading?
Reload with unparalleled speed, precision, and confidence using MARK 7® sensors. When you are loading on an automated press, it is almost impossible for you to keep track of every operation on each stroke. Did the case get decapped? Was your brass porperly primed? Is it properly swaged? Was the powder charge correct? Is the bullet seated correctly? Our advanced sensor technology empowers you to keep watch on all of these functions at all times, and each sensor will stop the press and alert you if it detects a problem. Designed to revolutionize your reloading experience, Mark 7 sensors allow you to achieve optimal performance with every press. Say goodbye to guesswork and hello to effortless reloading.
DecapSense
The Mark 7 DecapSense is designed to improve the reliability and safety of the reloading process. It ensures your machine stops and alerts you whenever a spent primer hasn't been removed during the decapping process, preventing potential damage to both you and your press.
How It Works:
At Station #2, the decapping process occurs, where the press pushes out the old primer from the brass case to prepare for a new one. The DecapSense uses an optical sensor to detect whether or not the spent primer has been successfully ejected. If the primer is missing or hasn't been removed, the machine will halt right before it moves to the next station, giving you time to check the impacted case. This feature helps prevent costly mistakes, as well as keeps your press running smoothly.
If you are working with new brass (which doesn't have primers yet), you can easily disable the sensor via the Mark 7 tablet interface, allowing you to reload without interruptions. The DecapSense also has the ability to detect whether brass is present at all in the decapping station—if there is no case, it can stop the machine before the press moves forward.
NOTE: Mark 7 Autodrive or Revolution Press required to use this sensor
Compatible with:
- APEX 10™/Evolution Autodrive™
- Revolution®
- Dillon RL1100/CP 2000/RL 1050/Super 1050 Autodrives
*Included with all 650/750 autodrives
SwageSense
The Mark 7 SWAGESense™ is designed to swage the toughest military crimped brass with ease, ensuring reliable results even with the most challenging cases. It also can detect both small and large primer ringers, especially those commonly found in wet-washed brass, and is capable of identifying small primers in .45 ACP brass. If the machine encounters a blockage or small pockets while using a large rod, it will automatically stop and alert you through the tablet. Additionally, it significantly reduces the likelihood of breaking swage rods, improving overall efficiency and durability. SWAGESense™ is constructed using hard anodized aluminum and comes complete with two hardened chromoly swage rods - for both small and large primer pockets.
How It Works:
During the swaging process, a specially designed rod is used to remove the military crimp and create a smooth, properly sized primer pocket. The SWAGESense™ system actively monitors this process, ensuring the swage rod enters the pocket correctly. If there are other obstructions—such as a partially ejected primer (a "ringer") or a smaller primer pocket—SWAGESense™ detects the issue and stops the press automatically, notifying you through the tablet interface. This built-in safeguard prevents damage to your equipment and ensures every case is swaged properly before moving forward.
Compatible With:
- APEX 10™/Evolution Autodrive™
- Revolution®
- RL1100/Super1050/1050X Autodrives™
- 650 Pro/750 Autodrives™
NOTE: Mark 7 Autodrive or Revolution Press required to use this sensor.
Primer Orientation Sensor
The Mark 7 Primer Orientation Sensor is designed to eliminate common issues with incorrectly placed primers while reloading. In the middle of a high-speed reloading session, you can often find out that primers will end up missing, upside down, or seated incorrectly, which is both frustrating and time-consuming. This sensor ensures the machine runs smoothly by automatically stopping it whenever it detects a problem with primer placement, helping avoid costly mistakes and keeping the reloading cycle on track.
How It Works:
The Primer Orientation Sensor works by monitoring the placement of primers in each case. As the brass moves through the reloading press, the sensor checks if each primer is correctly positioned. If the sensor detects that a primer is missing, upside down, crooked, or seated too high, it automatically stops the machine to prevent further issues. This saves you from wasting time and components, as well as maintain the overall quality of your reloads.
Additionally, the sensor has a second function: monitoring the rotation of the shellplate. If the machine fails to rotate the shellplate properly, it will trigger an alert and stop the press, ensuring that no steps are skipped or mishandled during the reloading cycle.
Compatible With:
- APEX 10™/Evolution Autodrive™
- Revolution®
NOTE: Mark 7 Autodrive or Revolution Press required to use this sensor.
Powder Check Sensor
The Mark 7 Powder Check Sensor is designed to ensure that every round reloaded during a cycle contains the right amount of powder. If the sensor detects a powder charge that's too high or too low, it'll automatically stop the machine and send you an alert on your tablet, prompting you to check the case. This helps avoid overcharged or undercharged rounds, ensuring the consistency and safety of the reloading cycle.
How It Works:
To use the Powder Check Sensor, you simply attach the appropriate probe (for small or large pistol, or small or large rifle cases) to the sensor rod. Then, adjust the sensor die to the correct height for your desired powder load. When the press is operating, the sensor probe is inserted into the case as it moves through the press. The probe’s position is measured using an infrared laser beam. If the powder level in the case falls outside the preset "overcharge" or "undercharge" limits, the sensor will detect the discrepancy and stop the press. You’ll receive an alert on the tablet, notifying you to inspect the case. The sensitivity can be adjusted based on the type of powder you're using and your specific needs.
Compatible With:
- APEX 10™/Evolution Autodrive™
- Revolution®
- RL1100/CP2000/Super1050/1050X Autodrives™
- 650 Pro/750 Autodrives™
NOTE: Mark 7 Autodrive or Revolution Press required to use this sensor.
BulletSense
The Mark 7 BulletSense is designed to prevent common loading issues before they impact your reloading process. Whether you’re dealing with missing bullets, upside-down bullets, or misaligned brass, the BulletSense ensures that each case is properly prepared for bullet seating. It utilizes a precise laser to monitor the bullet placement and can stop the machine if it detects a problem. It also acts as a brass sensor, ensuring no case is missed. BulletSense is fully adjustable to work with different bullet types and calibers, giving you peace of mind and preventing costly errors during your reloading session.
How It Works:
During the reloading process, bullets are placed on top of the case through a bullet feeder. As the shell plate moves, BulletSense uses a laser system mounted on an adjustable slider to detect the bullet's position. If the bullet is missing, upside down, sideways, or if there’s no brass present in the station, the laser beam will return to the sensor head uninterrupted, triggering the system to stop the machine. You’ll receive an alert on your tablet, prompting you to check the case. The height of the laser is easily adjustable using a thumb screw, giving you full control over where and how it detects the bullet and brass. This helps eliminate mistakes like improperly seated bullets, ensuring smooth and safe reloading.
Compatible With:
- APEX 10™/Evolution Autodrive™
- Revolution®
- RL1100/CP2000/Super1050/1050X Autodrives™
- 650 Pro/750 Autodrives™
NOTE: Mark 7 Autodrive or Revolution Press required to use this sensor.
Always Building Towards the Future
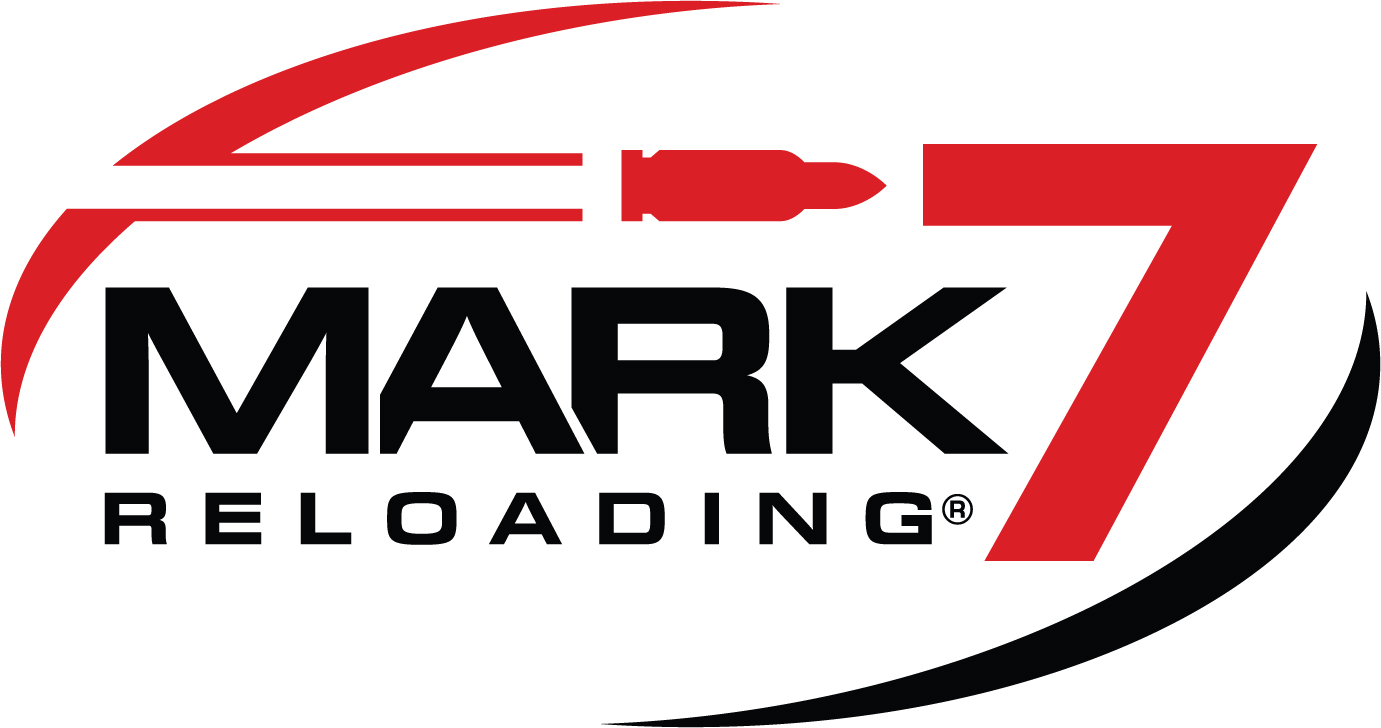
Always Improving
We stand behind our products. We are here for you with any help you may need - from setting up your machine, selecting the perfect accessories, to handling any problems.
If you have questions or problems, our customer support team is on call to answer anything and get you back up and running as quickly as possible.
We offer training classes, both at our locations, and even at your office or shop if requested. We can come and help you set up your systems and get you up to speed and cranking out ammo in no time.
If you’ve owned any Mark 7® machine for a few years, whether it is a Revolution®, an Evolution®, an Apex 10®, or an Autodrive®, we even offer an opportunity to send it back to us so we can install any new updates, and go over it with a fine tooth comb to be certain it is working at it’s very best for you.
For Consumer Website sales, Mark 7® is proud to partner with Sezzle to offer financing and interest free payment options for purchases on our website up to $15K.
Still Have Questions? Reach Out!
The Mark 7® Sales Team is always ready to help! Contact us if you need help selecting the best press for your needs or choosing the right equipment to get the most from it, or financing your purchase. Our sales team is available by phone from 8:00am - 5:00pm EST Monday - Friday. After hours, please send us an email and we will get back to you as soon as possible.